Autospire PERFORMANCE
Self-Propelled Mixer Wagon
The self-propelled diet feeder in the Autospire Performance range have capacities of 12 to 14 m3 in the single auger version and 16 to 24 m3 in the twin auger version. They have been designed for intensive use and have equipment dedicated to long tours, 40 km/h travel speed, Ecomode system and a hydraulic distribution box.
See features
Optimising feed costs and mechanisation costs are the main drivers of profitability on the farm. Lucas G has created a reliable, modern and efficient machine in line with precision breeding. From silo to trough to milk and meat, this succession of equally important steps must be measured and controlled to achieve precise and profitable production targets. These self-propelled machines are suitable for intensive use and have superior sound insulation for long journeys.
- Rear conveyor (right / left)
- Hydraulic offset of the feeding conveyor
- 2m width mill - 54 cutting sections
- Mill power 200 HP (except 120/140 156 HP)
- Loading conveyor with straight bars
- Hydraulic cut-off plate
- Ecomode System & Automotive system
- Programmable weighing unit
- Distribution box
The Autospire has a high ground clearance and can be equipped with 4-wheel drive and 4-wheel steering in order to be able to handle all groups of animals, regardless of the location of the buildings, the climatic conditions and the state of the farmyard.
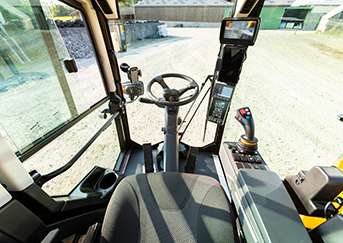
Several features have been added for additional operator comfort including a new ergonomic command arm and joystick, the option of a new pedal mode for driving and a new layout of the control screens. Operating comfort and visibility have also been enhanced with the addition of a new 360° panoramic glass cab for optimum working conditions and safety. The new cab is fitted as standard with a comfortable air seat, air conditioning, a sun visor and a front defrosting window, display, to retain the visibility benefits of the new cab.
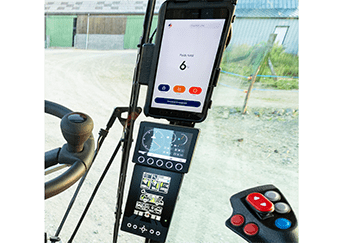

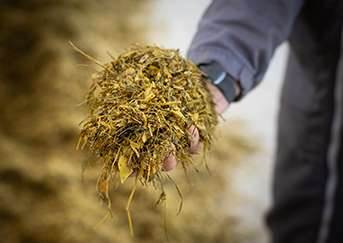
Material can move easier in a smooth rounded tank because it is not subjected to stress.As a result, the ration is mixed naturally and more effectively. The power required for a mix is reduced to a minimum. The smooth flared shape means that a homogeneous mixture can be obtained faster. The round design of the tank automatically extends the life of the tank.
The Lucas G stepped augers have a unique form which means that the ration can be cut and ventilated by the steps which ensures the rations are blended properly for optimal proportioning.In standard, augers come with 6 knives. It is possible to have 8 or 10 knives for each augers, adjust the angle to increase aggresivity and thus cut the fibre faster. The auger knives are tungsten carbide coated and are reversible to increase the lifetime.To speed up the cutting process, the cut-off plates with programmed sequences are inversed to facilitate blocking the fibre at the bottom of the tank.
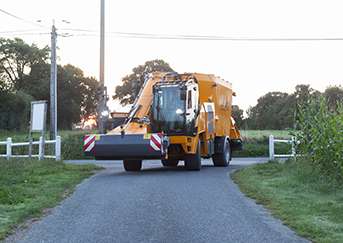
The Autospires PERFORMANCE are fitted with a series of 3 auger rotation speeds in order to adapt to the different feed material and to ensure distribution speed remains constant. The augers are hydrostatically driven which ensures easy and comfortable use.
- Smoothing speed 1-10 rpm
- Smoothing speed 2-23 rpm
- Fibre speed and emptying 45 or 60 rpm
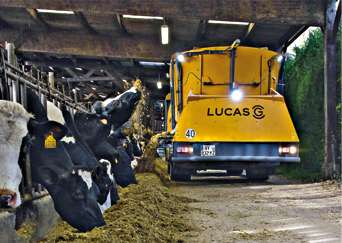
The large size of the distribution conveyor and the unloading trap door, mean that any jamming linked to fibrous rations can be avoided and a regular swath can be given along the feeding table. The speed of the conveyor is adjustable to perfectly control distribution. Thanks to the conveyor located at the rear of the machine, the distribution (left or right) is made regardless of space configuration even in dead end feeding alley. To guarantee optimal distribution efficiency, the conveyor distribution height is 800 mm and it can be hydraulically offset by 375 mm from left to right to the feed troughs.
The machines are equipped with heavy-duty tyres for optimum road holding and safety at 40 km/h. The front hydropneumatic suspension and rear parabolic blade suspension provide flexibility and driving comfort for the operator. Lucas G offers an ECOMODE system as standard on these machines. As soon as the machine exceeds 35 km/h, the system is automatically activated to set the engine speed at 1600 rpm instead of the original 2300 rpm, thus allowing a relative reduction in fuel consumption and a reduction in noise inside the cab.
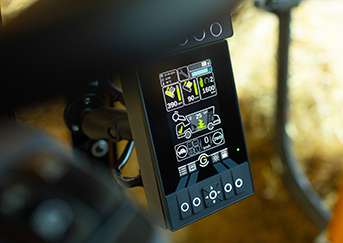
Depending on the material loaded, the operator can change the speed of the mill as well as the speed of the loading conveyor with a single touch of the screen via the XPA Display terminal. This function allows for the best possible handling of the different types of loaded products.
Our default settings:
- Concentrate speed: 50 % maximum. mill + 40 % max. conveyor
- Silage speed: 80 % maximum. mill + 80 % max. conveyor
- Fibre speed: 100 % maximum. mill + 100 % max. conveyor
The machine has been designed with an optimally positioned motor to avoid pressure drops:
- Unladen weight, 55% front and 45% rear.
- Loaded, 45% forward and 55% front.
The engine is centrally located on the right side and directly powers the main operating parts of the machine. This positioning limits pressure losses and guarantees responsible and efficient use of the machine.
The shape of the mill, coil design and position of cutting sections have been studied for better unloading and to reduce the negative effects of recycling (time wasting and shelling). The shape and angle of the coil means that the feed material is gathered, recentred and placed in the middle of the conveyor for increased output. The sections are placed behind the coil to cut the produce without upsetting the loading flow.